Aluminum-to-Copper and Rail Connections Without Compromising Steel Safety
The railway sector constantly faces critical challenges when creating reliable and durable aluminum-to-copper and rail connections. These connections are essential not only to ensure the continuous flow of energy but also to preserve the safety and integrity of railway infrastructure.
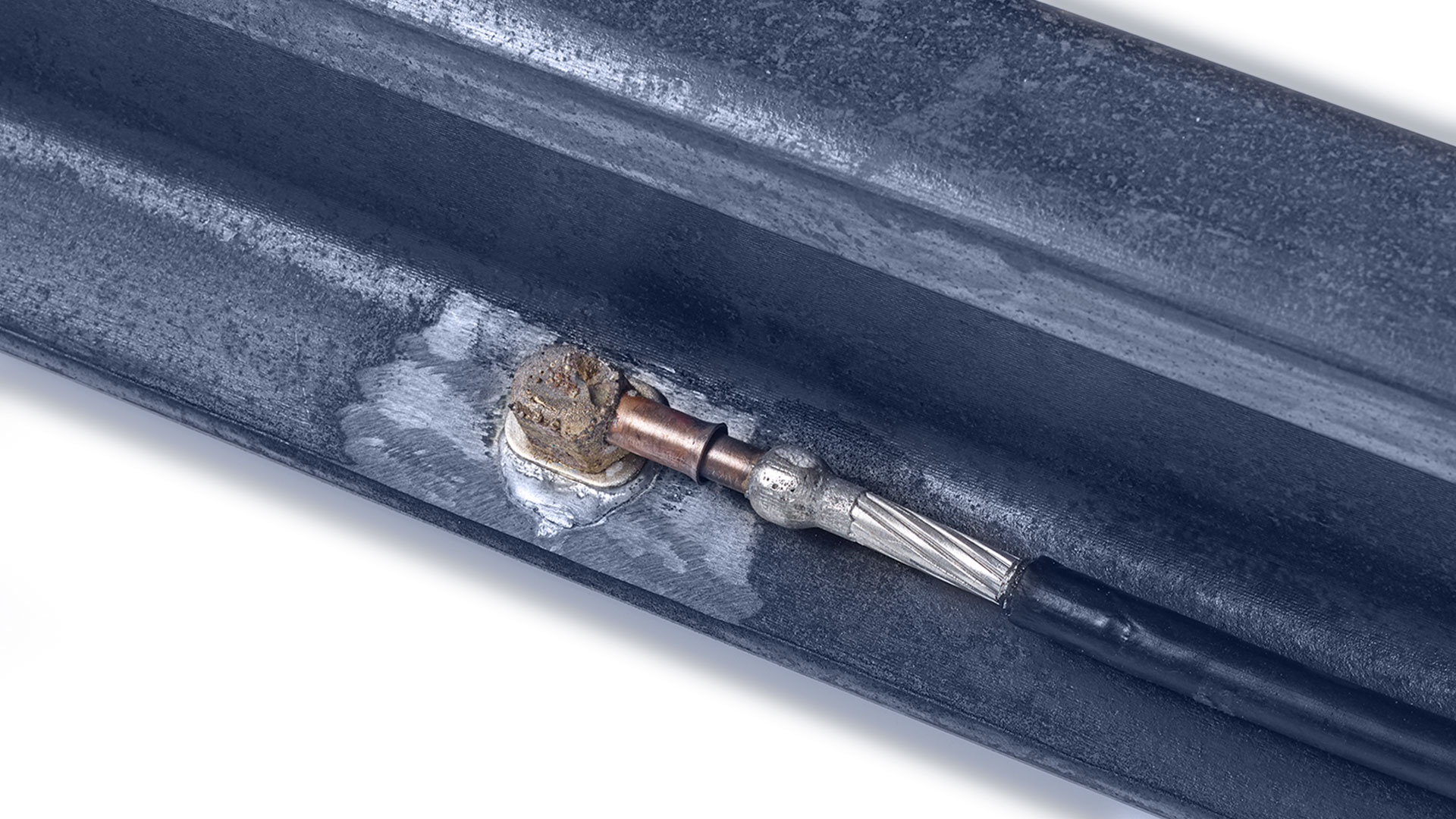
Does Not Damage the Steel Structure of the Rail
Common Issues in Railway Connections
- Joining different materials: Working with materials such as aluminum and copper can be challenging due to their distinct properties, making it difficult to achieve a robust and long-lasting connection.
- Risk of structural damage to the rail: Traditional methods, such as drilling or direct welding, can compromise the molecular structure of the rail, shortening its lifespan and increasing operational risks.
- High maintenance costs: Prematurely failing connections result in costly repairs and unplanned downtime.
These challenges not only increase operational costs but also pose a significant risk to the safety and efficiency of the railway system.
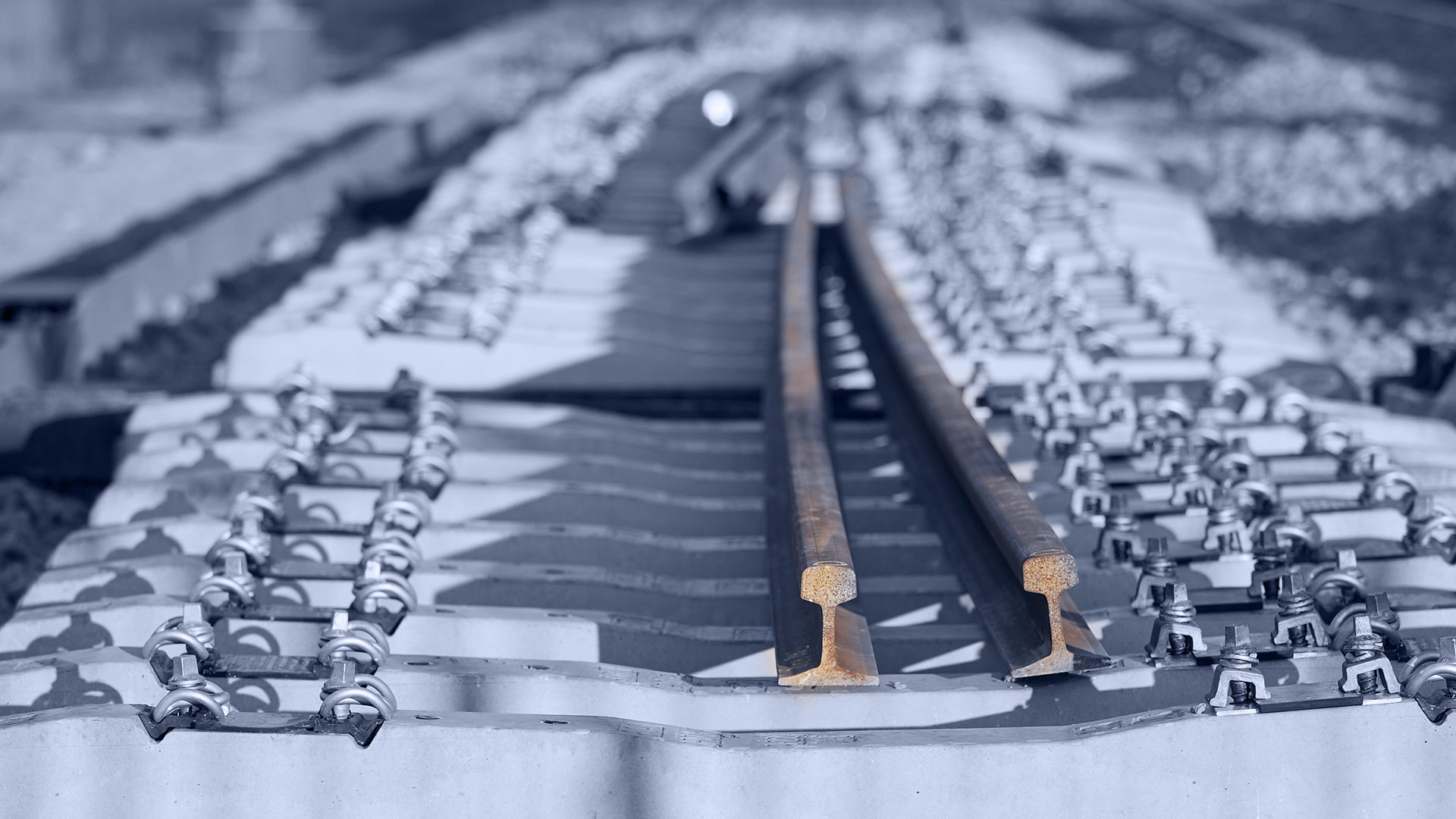
Different Joints
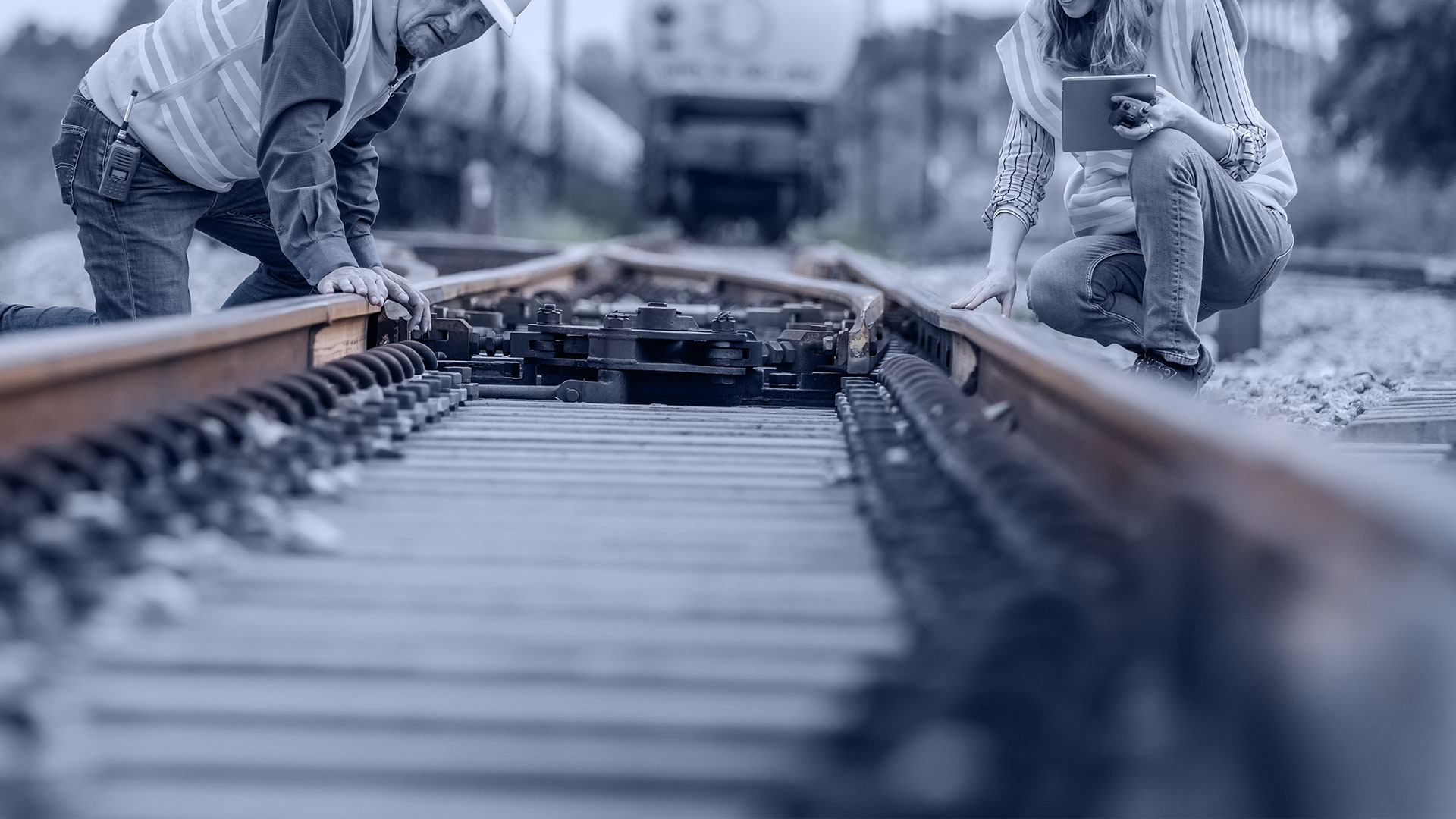
Structural Damage to Tracks
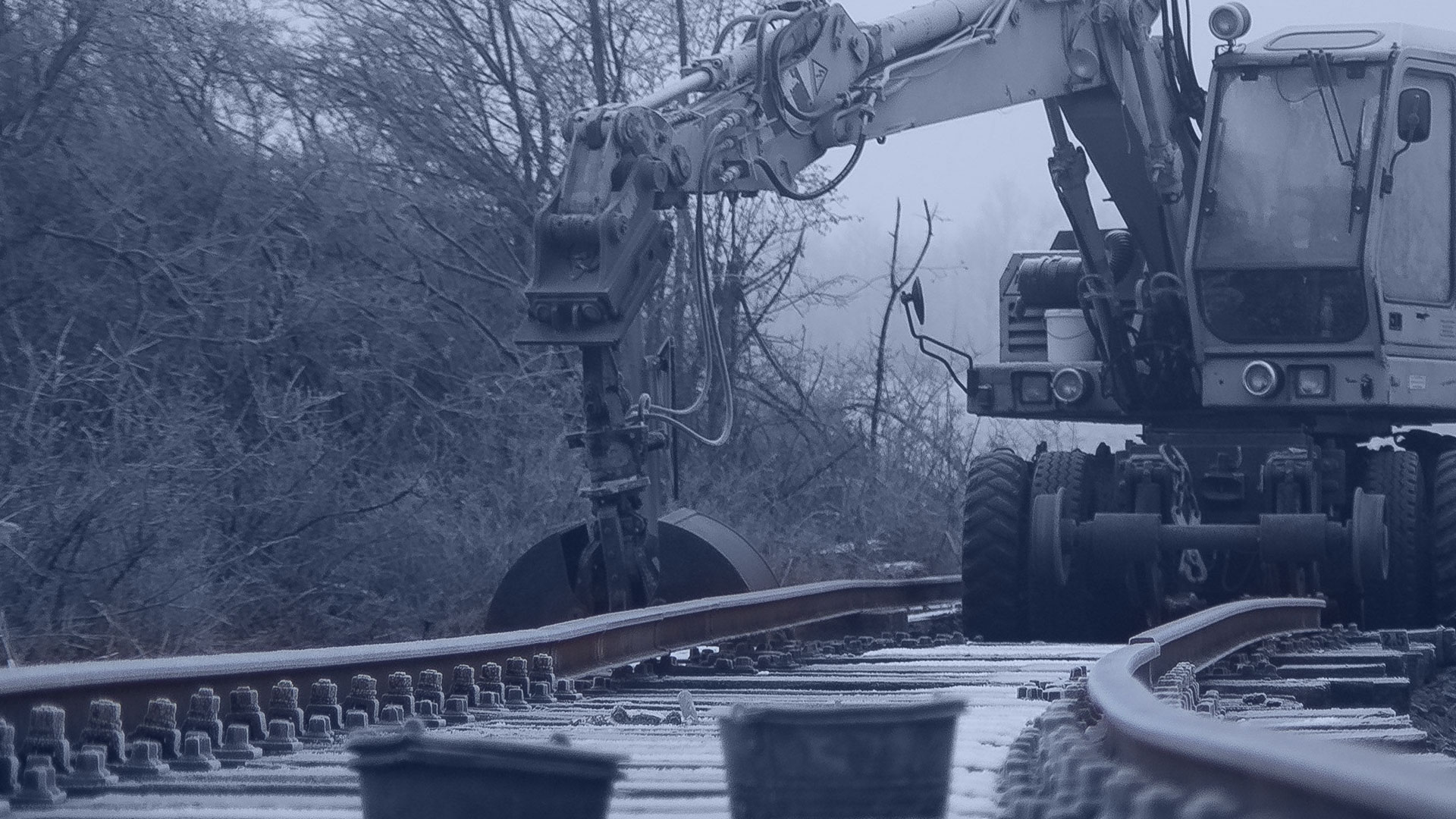
High Repair Costs
KLK’s Comprehensive Solution: InDuoAl + ELPA 12
At KLK Electro Materiales, we have developed an innovative solution that effectively addresses all these issues. Our approach combines two exclusive technologies: InDuoAl and ELPA 12, designed to provide safe, efficient, and durable electrical connections.
First Stage: Aluminum-to-Copper Connection with InDuoAl
The InDuoAl system utilizes specially designed exothermic welding for aluminum. This technology enables a molecularly perfect connection between aluminum cables and copper bolts, ensuring:
- High electrical conductivity: Ideal for critical applications in railway environments.
- Corrosion resistance: Extends the lifespan of connections even in adverse conditions.
This initial stage ensures that the aluminum-to-copper connection is solid and efficient, addressing one of the most significant technical challenges in the industry.
Second Stage: Bolt-to-Rail Connection with ELPA 12
The next stage utilizes the ELPA 12 system, which connects the copper bolt to the steel rail without the need for drilling or direct welding. This process includes:
- Use of a tin-coated steel plate: This plate acts as an intermediary, absorbing thermal shock and protecting the rail’s structure.
- Controlled temperature: The process does not exceed 600 ºC, preserving the molecular integrity of the steel.
The result is a secure connection that respects the rail’s structure while maintaining exceptionally low electrical resistance and high mechanical durability.
Key Benefits for Railway Sector Professionals
Choosing the combined solution of InDuoAl and ELPA 12 offers significant benefits:
- Infrastructure protection: Eliminates the need for drilling, preventing structural weaknesses.
- More durable connections: Designed to withstand extreme conditions and minimize maintenance costs.
- Time optimization: Systems are designed for quick and secure installation, reducing on-site work time.
Don’t let traditional issues compromise the efficiency and safety of your railway operations. With the unique combination of InDuoAl and ELPA 12, KLK delivers a revolutionary solution that redefines quality and durability standards in the sector.
Do You Have a Project That Needs Reliable and Customized Solutions?
Contact us, and we will develop the product that best suits your project.
Here Are Some Catalogs You Might Be Interested In:
KLK Electro materiales slu
Mail | Web | Teléfono | Chatbot | Social Media
Do you need help?